All Custom Ornamental Iron Fabricators are not Equal
Consider the following when you think about your ornamental fabrication needs.
How long has the company that you are entrusting with your high-end custom ornamental iron work been in business?
Six weeks? months? Six years? With Patina Metals, you get over 6 decades of experience and excellence in every product and service. We have withstood the test of time because we deliver quality and exceed expectations and not all Ornamental Iron companies are the same. Is the company you are considering meeting or exceeding the highest standards of NOMMA, or the National Ornamental and Miscellaneous Metals Association (NOMMA), the authority for ornamental metal? As a decades long member, Patina Metals always exceeds expectations as we strive to exceed the highest standard finish of NOMMA #1 weld finish standard, whereas the majority of Custom Iron companies fabricate using a combination of NOMMA #2 and #3 weld finish standards. Today, we will discuss just a couple of items specific to weld finish, malleable iron finishes, and common ferrous metal aspects in general. Next blog will focus in on non-ferrous metals, so check back!
I. Welding finishes. Patina Metals Standard Finish #1 as follows. Are you getting this level of finish for your jobs?
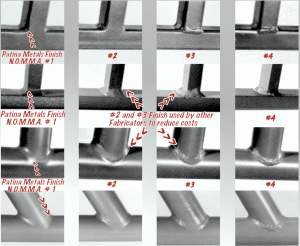
Raked Pipe: 1-1/2″ to 1-1/2″ pipe “T” RAKED Patina Metals Standard |
||
![]() |
|
![]() |
![]() |
![]() |
Pipe weld: 1-1/2″ to 1-1/2″ pipe “T” Patina Metals Standard |
||
![]() |
![]() |
|
![]() |
![]() |
Solid Square: 1/2″ square to 1/2″ x 1″ bar “T” Patina Metals Standard |
||
![]() |
![]() |
|
![]() |
![]() |
II. Malleable Iron
What about offering you better grades of malleable iron, instead of forcing the least expensive option on you, without giving you an option.
Fabrication finish options for malleable iron direct from the foundry have an irregular rough textured surface overall that reveals casting lines, voids, and other imperfections.
Patina Metals offers three finish grades for our malleable iron products:
Foundry Grade (FG) – As received direct from the foundry. High level of surface texture variations and high level of variation from piece to piece. These are not recommended for most applications, but you may not have that choice if you go with just any metal fabricator.
Commercial Grade (CG) – Pieces from the foundry are selected for job uniformity and the largest variations are cleaned up. Cast lines are still evident.
Architectural Grade (AG) – Commercial grade malleable iron that is cleaned up to a higher degree and sandblasted to minimize the surface texture variations.
Because of the irregularities that will be evident with any of the finish grades, we recommend a painted finish for all malleable iron products.
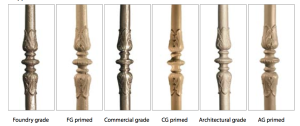
III. Ferrous Metal Finishes
It is well known that most substances tend to revert to their natural form, and among the architectural metals, carbon steel and iron are the most conspicuous examples of this rule. All of the common metals oxidize, or corrode, to some extent, but while the oxides forming on other metals generally inhibit the progress of further corrosion, the oxide, or rust, that forms on ordinary carbon steel and iron does not act in this way. Instead, if not prevented, oxidation progresses until the metal reverts to essentially the same state in which it was found in nature.
It is generally the chief function of the finishes used on the common ferrous metals to counteract this tendency, to inhibit corrosion. Some of the high strength, low alloy, copper bearing structural steels have been used in exposed applications such as building structural elements, curtain walls, bridge structures and transmission towers without applying paint for surface protection. These steels are referred to in the industry as “weathering steels.” When exposed to the weather they develop a relatively tight, adherent oxide film that tends to protect the surface against further oxidation or rusting, with time the film darkens and takes on a color ranging from dark reddish brown to a warm purple black. These surfaces, however, are not fully resistant to the effects of rain and serious rust staining can occur where water runs down and off the building on materials such as concrete. While exposed surfaces have excellent durability, unexposed surfaces and interior surfaces do not develop sound oxide films and must be cleaned and painted with rust inhibiting primers in the same way that other carbon steels are protected. Today these steels are not often used for architectural applications. The term “finish,” when used in reference to iron and steel, usually has a somewhat different connotation than when used in reference to the nonferrous metals. On the other metals it generally implies a surface treatment by mechanical or chemical means, and less frequently refers to an applied coating of some kind. Below we have an example of a powder coating layer applied to a metal substrate.
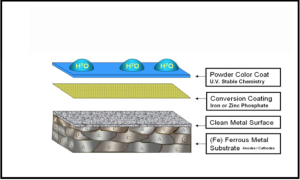
With iron and steel the reverse is true- most of the common finishes used on these metals are applied as coatings. Mechanical and chemical processes are extensively used for cleaning and surface preparation, but rarely as true finishes. All types of additive coatings are used far more extensively on carbon steel than on other architectural metals, and for two basic reasons: 1) a protective covering is usually essential, as already explained, and 2) if an opaque coating is to be used on a metal it is only the coating itself which is seen, and for many applications costs can be minimized by using the most economical substrate having the necessary physical properties. The ferrous metals satisfy this requirement. It should be noted, however, that the durability of many organic coatings under exposure to the elements is influenced by the durability of the base metal itself. Deterioration of the coating may be initiated at the interface between the coating and the substrate, due to the penetration of the coating by corrodents, and the corrosion resistance of the base metal therefore becomes a critical factor.
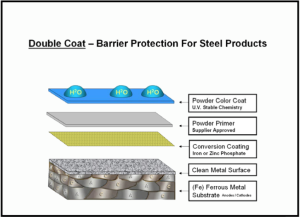
Probably the most common finish for architectural steel and iron is paint, a form of organic coating, applied by brush, spray, flow coating or dipping and frequently air dried. Relatively inexpensive metallic coatings of zinc, aluminum or combinations of these two metals, are applied to many steel building products, serving either as a base for subsequent organic coatings or as a final finish. Vitreous coatings in the form of porcelain enamel and plastic films as laminated coatings are also used. With the exception of some hardware items, metallic coatings are not used on architectural products made of aluminum, copper alloys or stainless steel. On the other hand they are commonly applied to carbon steel and iron. For this reason metallic coatings are discussed in this section. We will go more in depth on finishes for Ferrous and Non-ferrous metals next blog.